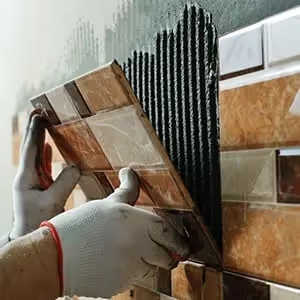
Particle Size Reduction & Distribution in the Ceramics Industry
Particle size reduction and distribution is crucial to manufacturing ceramics, and manipulating the transport, mechanical properties and densification of oxides and minerals (e.g. aluminum oxide to zirconium oxide). Particle sizes range fairly broadly, from smaller than 100 nm to more than 100 µm.
Particle Size Reduction & Distribution for Electronic Materials
The electronic materials industry uses ceramic, metal, alloy and oxide powders in a variety of applications. Whether manufacturing a single crystal, film or paste; particle size reduction and controlled dispersion of these powders significantly enhances their dielectric, resistive and conductive properties. This is done through improved particle packing, increased homogeneity and improved mechanical properties (eg. better green strength and reduced porosity in barium titanate slip)
Particle Size Reduction & Distribution for Fuel Cells
Engineers rely on particle size reduction and distribution in order to control the chemical and physical properties of solid oxide fuel cells (SOFC) starting powders, as well as overall fuel cell performance (eg. such as compsite cathodes manufactured from LSCF and either GDC or SDC). Final porosity, transport properties and thermal expansivity can all be manipulated by controlling the starting particle sizes of these powders. The goal is to find cleaner and more efficient ways to produce electricity that alleviates dependence on coal and oil.
Particle size Reduction for Powders and Mixtures
Particle size reduction and controlling distribution is widely used in ceramics, electronics, fuel cells and other industries. Materials such as alumina (aluminum oxide), iron oxide, PZT (lead zirconium titanate), engineered solar glass and bio glass powders are commonly used in a variety of ceramics and can be some of the most difficult to process.
To achieve successful particle size reduction and distribution, it is necessary to generate forces directly to the individual particle. This can be done in a variety of ways. However as these high tech industries require a trend toward smaller particle sizes, current methods of processing become more expensive and less efficient. Many technologies tend to waste significant energy that is absorbed by the grinding media; or lose the precision to effect the individual particle when processing down to and below 1 micron.
BEE homogenizers have been creating sub-micron and nano materials with pharmaceutical powders and emulsions for 20 years.
Pion Chemical Process Equipment
At Pion, our chemical process equipment is used by customers in the ceramics industry to improve a wide range of materials by expanding their capabilities, and creating more diverse reactions.
Specifically, our particle size reduction homogenizer technology creates more consistent emulsions and dispersions with a tighter distribution of smaller particles which:
- increases surface area
- improves chemical reactions
- reduces the quantity of costly components
- eliminates the need for volatile organic compounds (VOCs)
- maximizes particle packaging
- increases dense cross section of final products
- improves particle coating during formulations
- increases conductivity
- creates a smoother surface quality and reduced porosity
- allows for finer printed features
In addition, our modular technology offers unique processing setups that solve specific processing challenges, such as: dual feed for addition of secondary additives, abrasive materials or catalysts; dual jets to increase impact velocities for hard materials; and high viscosity chemical process equipment solutions up to and above 100,000 cPs.