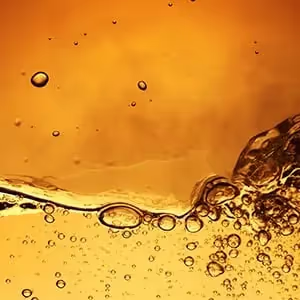
Fossil fuels fill a critical need in our worldwide economy, yet their combustion produces both nitrous oxide (NO) and particulate matter (PM) emissions. However, emerging technology around alternative fuels has yielded the emulsion fuel, which has the ability to reduce greenhouse gases and is a more efficient fuel source. This novel technology will allow humans to continue enjoying many of our modern-day comforts while better preserving the environment we exist within. Interestingly, because emulsion fuel is comprised of water droplets dispersed in an oil phase, the mixture needs to be produced through powerful mixing. (1) Here we analyze advantages of using high pressure homogenization as the emulsion fuel production method.
- Ability to Achieve Chemical Stability
An emulsion is classically defined as a mixture of two immiscible liquids. Emulsion fuels, for example, contain both water and oil, and these normally incompatible fluids are expected to mix and remain mixed. Microemulsion-based fuels, although found on the market, have been largely unsuccessful because they require such high levels of surfactant that the fuel is essentially ineffective. Nanoemulsion-based fuels, however, require less surfactant so hold more promise for potential use. Because stable nanoemulsion production requires high shear, high pressure homogenization is strongly recommended.
- Production of Fine Particles
Aside from its biochemical composition, particle size has perhaps the biggest influence on a product’s function. Multiple studies have shown that smaller particle sizes enhance product effectiveness. For example, among pharmaceutical products, this translates to increased bioavailability, and food and beverage products see enhanced appearance and extended shelf life. Emulsion fuels, as well, see benefits in that as the size of the dispersed particles decreases, the solution’s chemical stability (see above) increases. High-pressure homogenization in particular has the ability to reduce particle size to levels that are not achievable by most other mixing processes. (2)
- Reduced Costs & Harmful Emissions
You may be wondering how emulsion fuel production costs can be reduced when you need to invest in a high pressure homogenizer. In the long run, using a high pressure homogenizer allows for significant savings on surfactant that would need to be used in the absence of a high pressure homogenizer. And of course, the reduction in harmful emissions is critical to the success of this alternative fuel. NO emissions can be reduced by up to 35% and PM emissions can be reduced by up to 60%, all because emulsion fuels burn completely than diesel fuel.
Pion: Equipment For Emulsion Production
As you either embark on or continue along the process of producing emulsions, your product’s success may depend on the equipment used to make it. High pressure homogenization is the most common method for producing emulsions, because of both its powerful mixing process and its cost/time effectiveness. The homogenizer will shear fluid by forcing it through a restrictive valve, forming a an emulsion with decreased particle size. Pion's BEE brand technology is trusted by lab managers and scientists around the world for their high-pressure homogenizers. They offer homogenizers that are both high-quality and reliable, and which can help your lab produce nano/micro emulsions, dispersions, and suspensions to be incorporated into your pharmaceutical cream. Visit us here to learn more about our products.